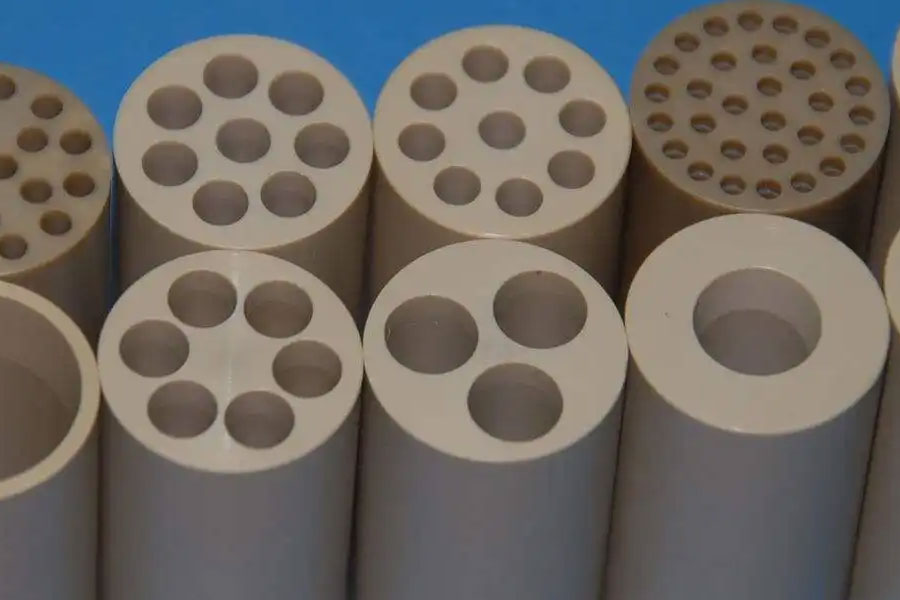
Plastic raw materials are divided into two types: thermosetting plastics and thermoplastics. Our existing injection molding materials usually refer to thermoplastics. Thermoplastics can be divided into two types: crystalline and amorphous according to the structural characteristics of their internal molecules. Crystalline polymers The internal molecules are arranged in an orderly and regular manner, with obvious melting points such as PE, PP, POM, PBT, PET, PA; the internal molecules of amorphous polymers are arranged in disorder, and there are no obvious melting points such as PS, ABS, PVC, PMMA, PSU, PPO. The following is a brief introduction to the material characteristics of several commonly used plastic raw materials PP, POM, PC, PBT, PA6, PA66, ABS, PMMA and the precautions in the molding process:
- POM (polyoxymethylene) is a heat-sensitive plastic with a melting point of 165°C. It will decompose seriously at 240°C, and its color will turn yellow. The residence time at 210°C should not exceed 20 minutes, and it will be heated within the normal heating range. After a long time, it will decompose. After decomposing, there will be a pungent smell and tearing. The product is accompanied by yellow-brown stripes. The density of POM is 1.41—1.425. ℃+0.5℃, the drying time is 3-5 hours, the injection pressure is generally increased to increase its fluidity in production, if there is decomposition or PVC, AAS and other materials in the barrel, the barrel should be cleaned in time clean.
- The melting point temperature of PP (polypropylene) is 164℃—170℃, the thermal stability is good, and the decomposition temperature can reach above 300℃. In the case of contact with oxygen, it begins to yellow and deteriorate at 260℃, and the molding shrinkage rate is relatively high. It is large (1-1.5%), and has anisotropy. It is easy to warp or twist due to molecular orientation during low temperature molding. The density is 0.91, which has good folding performance. The resin particles have a waxy texture, and the average water absorption is less than 0.02 %, the allowable content of molding moisture is 0.05%, so drying treatment is generally not performed during molding. If the moisture content is too high, it can be dried at about 80 ° C for 1-2 hours. more sensitive.
- PC (polycarbonate) begins to soften at 215°C, begins to flow above 225°C, and the melt viscosity below 260°C is too high, and the product is prone to insufficiency. The molding temperature is generally selected between 270°C and 320°C. ℃ will decompose, the drying temperature is between 120 ℃ and 130 ℃, and the drying time is more than 4 hours. The PC resin is generally colorless and transparent particles. Note that if there is PVC or POM in the barrel during production, do not When feeding directly to heat up, the barrel should be cleaned with PE resin for reproduction. The molding process should be multi-stage injection, the mold temperature is 80℃—130℃, and the special screw is used.
- PBT (polybutylene terephthalate), the melting point is 225℃—235℃, the decomposition temperature is around 280℃, the molding temperature is generally selected between 240℃—260℃, and the drying temperature is Generally, it is 120℃—140℃, and the drying time is 3—5 hours. PBT resin is generally white particles. The mold temperature is above 100℃, which has strong heat sensitivity, easy to overheat, and easy to remove powder. The mold cavity must be cleaned frequently.
- PA6 (polyamide) commonly known as single six nylon melting point is 215 ℃—221 ℃, 310 ℃ begins to decompose, drying temperature is 90 ℃ — 100 ℃, drying time is 5—6 hours.
- ABS plastic is a terpolymer made of three monomer components, acrylonitrile (A), butadiene (B), and styrene (3) by graft copolymerization. The molding temperature is generally above 160 °C, The color starts to turn yellow at about 250°C, and begins to decompose above 270°C. The resin is generally light ivory opaque particles. The drying temperature is 80°C—85°C, and the drying time is 2—4 hours.
- PA66 (commonly known as double six nylon), the melting point is 260 ℃ — 265 ℃, it begins to decompose at about 310 ℃, and the drying process is the same as that of nylon 66. The temperature of PA resin is too high, which may cause the material to change color and yellow, and PA resin generally It is white, translucent or opaque particles. When molding, it is necessary to control the temperature of the nozzle or use a self-locking or nozzle to prevent drooling.