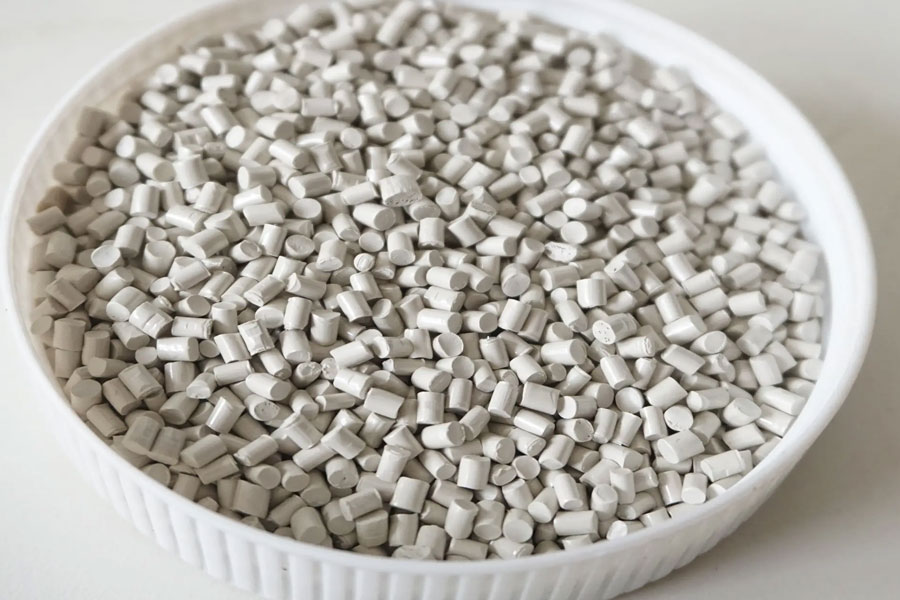
Greater Compatibility
Compatibility is the fourth factor that determines the quality of black masterbatch. If the masterbatch is produced from chips or recycled material, it may contain contaminants or other non-meltable polymers. This can cause unforeseen, unmanageable troubles, wasting the end consumer’s time and materials. At this time, primer resin can be used to produce high-quality color masterbatch, and the masterbatch has good compatibility during the melting process. High quality masterbatches can be produced using LLDPE, LDPE, HDPE, PP, PS, SAN, PA and other materials. Special polymeric masterbatches are available if engineering grades and stringent physical properties are specified. Several international large-scale color masterbatch manufacturers are conducting research to produce the so-called “global universal” color masterbatch. These masterbatches can be widely mixed with other raw materials, have good rheology, and can be used flexibly.
Strong Coverage
The second factor that determines the quality of black masterbatches is covering power, and this factor is especially important for masterbatches used in scrap or recycled polymers, where the role of black is to cover other materials in the scrap. color. Large particle carbon black has poor tinting ability and is not easy to cover all other colors in the lower layer. As a result, the final product only gets a deviated color. The ability to correctly select a carbon black with a high tinting power to cover the existing color during the melting process is the so-called covering power.
The Degree Of Dispersion Should Be High
Black masterbatches are produced using carbon black. Raw carbon black is a very difficult and dirty mixture, it is dusty, light and fluffy. Unless large-scale treatment is used, it can foul machines and workers, making the work environment filthy. Because of this, casters generally choose to complete the pre-dispersion of carbon black on a resin carrier, that is, black masterbatch. This resin carrier is clean, free flowing and easy to use. In addition to being dirty, carbon black has a characteristic that it is difficult to disperse. If the raw carbon black is melted directly during injection molding, the coloring effect will be very poor. Carbon black streaks and speckled areas with no dispersion are clearly visible next to less pigmented areas. Standard injection molding machines cannot effectively disperse green carbon black.
The difficult-to-dispersion properties of carbon black also plague color masterbatch manufacturers. The dispersion of high-load black masterbatches produced using single or double screw extruders is very poor. When the end user mixes or molds these black masterbatches, it performs only slightly better than carbon black, but the results are just as unsatisfactory. To achieve a stable high dispersion, a high-quality shear mixer must be used to compound carbon blacks, such as FCM or BANBURY blends. With sufficient strength, these mixers can fully mix the carbon black and base resin together. The type of carbon black used also affects dispersibility. The smaller the carbon black particles, the harder it is to disperse.
Better Liquidity
The third factor that determines the quality of black masterbatch is rheology and flow. If a color masterbatch itself has good dispersion, but it cannot flow into the material to be molded, the production effect is not ideal. In general, primer resins used to produce masterbatches have higher rheological properties. To save costs, some masterbatch producers use reusable materials, scrap or recycled materials as resin carriers. The flow properties of the masterbatches produced in this way will be significantly reduced, and if the rheology is not good, the mold will have trouble with cycle times and cosmetic handling. It is worth noting that if the dispersion and rheology are not high, some end users will compensate by increasing the dilution ratio, but this approach will only increase the cost of using the masterbatch. Masterbatches with minimal dilution ratios produce uniform, well-dispersed blacks.